Why you should choose Cap Compression Machines?
Cap Compression Machines outperform the Injection Molding Machines are more efficient, energy conserving, cost friendly and produce high-quality products as compared to Injection Moulding Machines. They are less impactful to the environment, need less materials, give a superior, smooth finishing cap without injection holes.
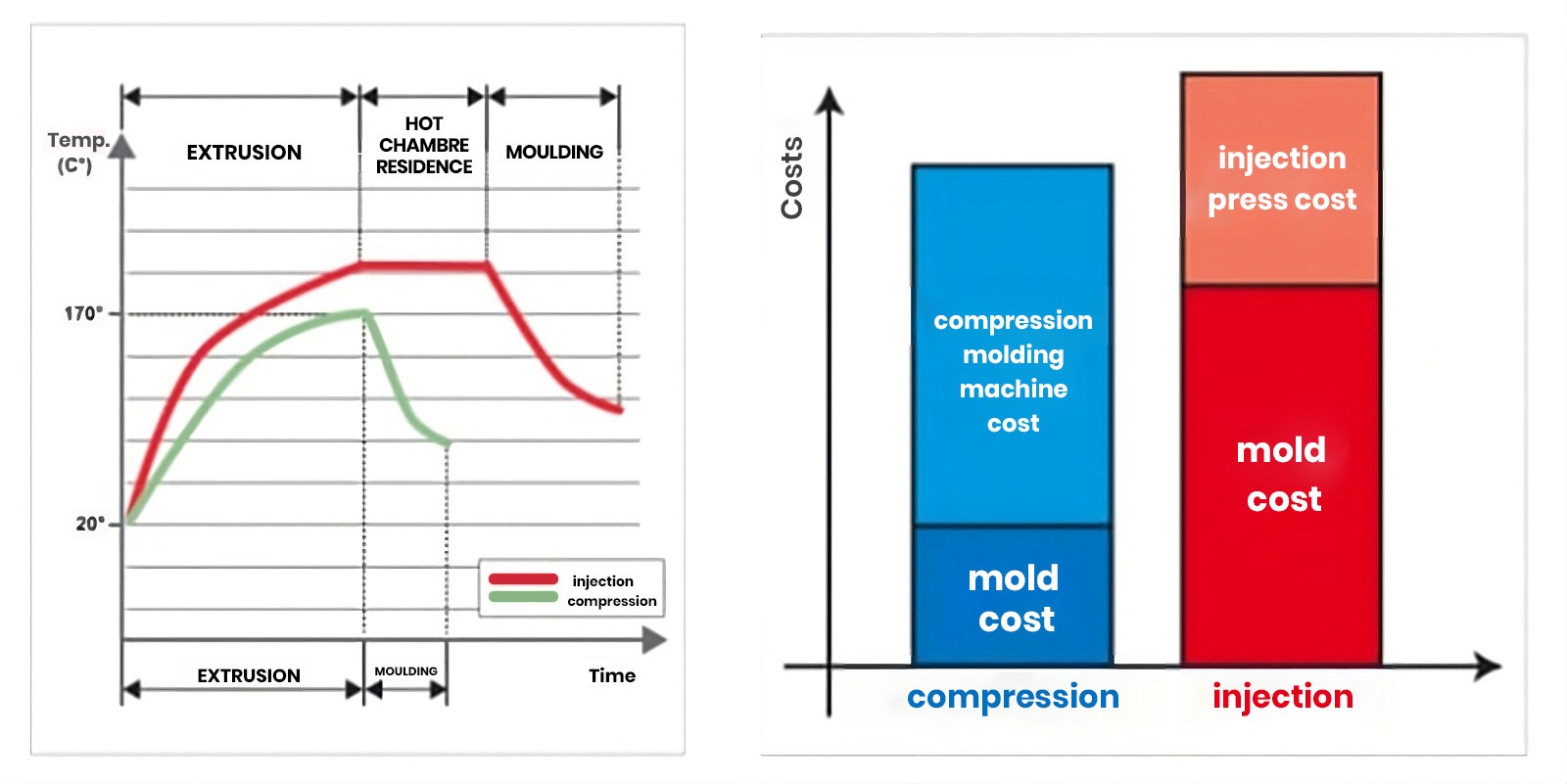
- Shorter Cycle Time and Higher Productivity: The lower extrusion temperature also give the benefit that the cap can be cooled faster in the mold cutting down the cycle time greatly. While it may take as little as 2 seconds when producing convection lightweight caps.
- Reduced Energy Consumption: With low extrusion temperature, the power consumed in preheating the plastic and cooling its temperature is also little. This leads to energy efficiency of between 35-45 percent reduction of energy per cap.
- Higher Specific Density: However, at lower temperature the same molding pressure gives a higher specific density and has no stress caused by an injection point. Instead, this leads to the better mechanical characteristics and the homogeneity that cannot be obtained using injection molding.
- Enhanced Consistency: When it comes to varieties of products to consumer in high speed like beverages it is necessary to have a constant supply to avoid jamming. The indicated plan ensures the stability of the cap production process to the necessary degree of reliability.
- Maintenance-Free Molds: In the compression molding, there are up and down and back and forth movement which does not affect the molds In the same manner, the compression molding can produce the same molds for decades before they get deformed due to their weights which make the injection molds to wear out.
- Quick Colour Changeovers: In comparison to colour changes in injection moulding whereby you have to clean the hot chamber and therefore colour changes take a lot of time, colour changes here do not undue a lot of time as they do not clean the hot chamber.
Related products
Why Choose Our Cap Compression Machine:
- Advanced Production Equipment and Improved Management System: We have installed Hi-tech equipment for mold and machine part so as to fulfil total production demand for our factory. Therefore, since all part manufacturing is performed within our workshop, the process can be centralized and the part produced is fully compliant.
- Experienced Technicians and Focused Leadership: Our staff includes a boss, who owns the business, and this person is the technician with the great clarity regarding mold and machine technology. He has spent a lot of time and capital on researching the efficiency models of World Class factories and has committed a significant number of resources in new product realization process. This environment however remains favourable to us because it means better maintenance of quality due to an assignment of concrete tasks and responsibilities at product improvement.
- Reliable After-Sales Service Team: After sales technicians’ team need six full-time technicians to ensure the customers are served well in after sales services. These experts are is in a position of moving from one corner of the world to another so that they can provide installation services, training and most importantly technical support once the machine has been purchased.
- In-House Mold Production for Perfect Fit: They have been in the business of mould manufacturing for more than two decades and as such their moulds suit the machine perfectly well including the next maintenance session.
- Collaborative Development with Siemens on Electrical and Control Systems:Our cap compression machine hydraulic oil and PLC control system, the program was developed through the cooperation of Siemens. In contrast of the conventional factories where various parts of the components are assembled using components bought from different suppliers, Siemens gives solutions for the entire automation technology range of PLC systems, connectors, and wires to ensure compatibility and efficiency.
Packaging and Shipping:
This might also be a good time to invite our technicians to your factory and to teach you how the machines work when installing them. However, all travelling expenses including air fare, accommodation and other service charges are incurred by the buyer.
After-Sales Support:
Every product conforms to export quality and standard packaging methods.
Delivery Time:
Delivery normally takes place 80-90 days after the depositor has made their purchase in their new home.
Shipping Port:
Products will originate from Ningbo, in the People’s Republic of China.